Dr Connie Qian
School of Mechanical, Aerospace and Civil Engineering
Senior Lecturer in Composites
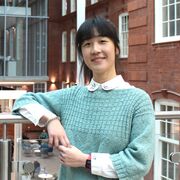
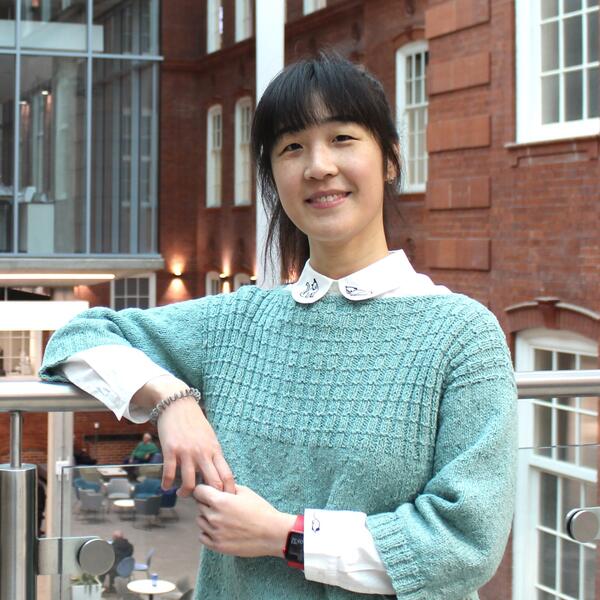
Full contact details
School of Mechanical, Aerospace and Civil Engineering
D18
Royal Exchange Building
64 Garden Street
Sheffield
S1 4BJ
- Profile
-
I study the deformation of composite materials using computer modelling and simulation.
Dr Connie Qian
Senior Lecturer in Composites
I grew up in China and came to study in the UK in 2005. I graduated with a 1st class BEng in Mechanical Engineering in 2009 and then a PhD in Mechanical Engineering in 2014, both from the University of Nottingham. My PhD was on RVE modelling and structural optimisation for discontinuous carbon fibre composites.
After completing my PhD, I stayed at the University of Nottingham as a Research Fellow from 2014-2018, during which I developed process simulation models for composites sheet forming, injection moulding, and thermoplastic overmoulding.
In 2018, I joined WMG at the University of Warwick as a Research Fellow and was later appointed as Assistant Professor in 2021, where I developed process simulation models for high-pressure RTM, double-diaphragm forming and compression moulding. My research vision started to shape during my time at WMG, as I became strongly interested in integrated process-property-performance simulation for compression moulded discontinuous fibre composites and hybrid architecture composites.
I joined the University of Sheffield as a Senior Lecturer in Composites in 2024 and in my spare time, I play the piano and the violin, and foster cats for the Blue Cross.
- Research interests
-
My research focuses on process-structure-property-performance modelling for fibre reinforced composites. I am particularly renowned for my research in high-volume manufacturing of discontinuous fibre composites, and have led several funded research projects in this area, notably an Innovation Fellowship funded by the EPSRC Future Composites Manufacturing Hub. I also have strong experience in applied research and have delivered large CR&D projects with industrial partners across the whole composites supply chain. I'm most active in the automotive domain, and have worked with some of the world's most-respected OEMs such as Jaguar Land Rover, Ford and Aston Martin.
My research interests are:
- Composites manufacturing process simulation
- Multi-scale modelling for composites
- Structural simulation and structural optimisation
- High-volume composites manufacturing processes
- Publications
-
Journal articles
- Numerical simulation for squeeze flow behaviour of carbon fibre sheet moulding compound. Composites Part A: Applied Science and Manufacturing, 199, 109241-109241.
- Repeatability and reproducibility of the measurement of prepreg tack following ASTM D8336: Results of a round-robin study. Composites Part A: Applied Science and Manufacturing, 188, 108561-108561.
- Experimental process characterisation for high-volume compression moulding of hybrid-architecture composites. Composites Part A: Applied Science and Manufacturing, 181, 108137-108137.
- Experimental and numerical investigation of the intra-ply shear behaviour of unidirectional prepreg forming through picture-frame test. Composites Part B: Engineering, 266, 111036-111036.
- Effective X-ray micro computed tomography imaging of carbon fibre composites. Composites Part B: Engineering, 258, 110707-110707.
- Experimental and numerical characterisation of fibre orientation distributions in compression moulded carbon fibre SMC. Plastics, Rubber and Composites, 51(8), 436-444.
- Finite element study of the microdroplet test for interfacial shear strength: Effects of geometric parameters for a carbon fibre/epoxy system. Journal of Composite Materials, 52(16), 2163-2177.
- 3D geometric modelling of discontinuous fibre composites using a force-directed algorithm. Journal of Composite Materials, 51(17), 2389-2406.
- Structural optimisation of random discontinuous fibre composites: Part 2 – Case study. Composites Part A: Applied Science and Manufacturing, 68, 417-424.
- Structural optimisation of random discontinuous fibre composites: Part 1 – Methodology. Composites Part A: Applied Science and Manufacturing, 68, 406-416.
- Finite element modelling of the flexural performance of resorbable phosphate glass fibre reinforced PLA composite bone plates. Journal of the Mechanical Behavior of Biomedical Materials, 15, 13-23.
- Representative volume elements for discontinuous carbon fibre composites – Part 2: Determining the critical size. Composites Science and Technology, 72(2), 204-210.
- Representative volume elements for discontinuous carbon fibre composites – Part 1: Boundary conditions. Composites Science and Technology, 72(2), 225-234.
- Notched behaviour of discontinuous carbon fibre composites: Comparison with quasi-isotropic non-crimp fabric. Composites Part A: Applied Science and Manufacturing, 42(3), 293-302.
- A failure mechanics study of aligned brick-and-mortar discontinuous long-fibre composites. Journal of Thermoplastic Composite Materials.
- Quality Analysis of Weld-Line Defects in Carbon Fibre Reinforced Sheet Moulding Compounds by Automated Eddy Current Scanning. Journal of Manufacturing and Materials Processing, 6(6), 151-151.
Conference proceedings papers
- The first European benchmark exercise on squeeze flow testing of high-performance carbon fibre sheet moulding compounds. Materials Research Proceedings, Vol. 54 (pp 676-685)
- Experimental characterisation for compression moulding of hybrid architecture composites using reclaimed prepreg manufacturing waste. Materials Research Proceedings, Vol. 41 (pp 631-640)
- A Comprehensive Assessment of Commercial Process Simulation Software for Compression Moulding of Sheet Moulding Compound. ESAFORM 2021
- Numerical and Experimental Studies of Multi-ply Woven Carbon Fibre Prepreg Forming Process. Procedia Manufacturing, Vol. 47 (pp 93-99)
- Flow characteristics of carbon fibre moulding compounds. Composites Part A: Applied Science and Manufacturing, Vol. 90 (pp 1-12)
- Establishing size effects in discontinuous fibre composites using 2D finite element analysis. Computational Materials Science, Vol. 64 (pp 106-111)
- Flow Behaviour of Carbon Fibre Sheet Moulding Compound. Key Engineering Materials, Vol. 926 (pp 1350-1357)
- Numerical simulation for squeeze flow behaviour of carbon fibre sheet moulding compound. Composites Part A: Applied Science and Manufacturing, 199, 109241-109241.
- Teaching activities
-
MEC313 Finite Element Techniques