Dr Linwei He
School of Mechanical, Aerospace and Civil Engineering
Lecturer in Structural Engineering
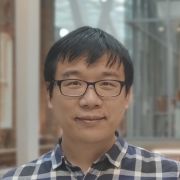
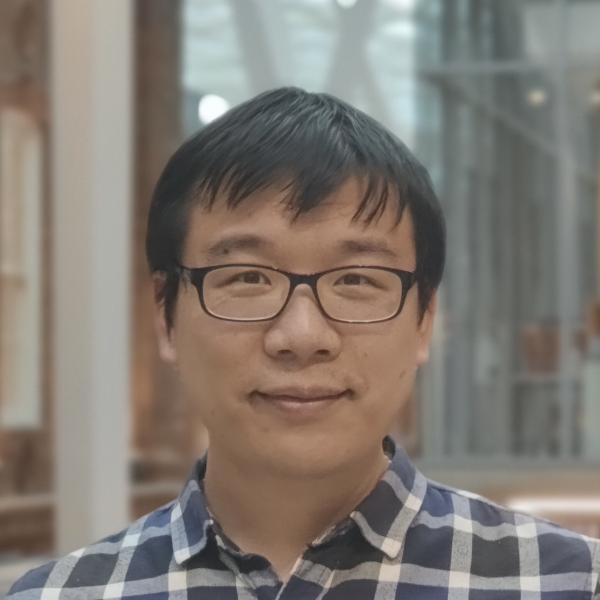
Full contact details
School of Mechanical, Aerospace and Civil Engineering
F113
Sir Frederick Mappin Building (Broad Lane Building)
Mappin Street
Sheffield
S1 3JD
- Profile
-
I use optimisation in structural design and analysis to reduce the carbon footprint in new buildings as well as to protect and repair existing structures.
Linwei He
Linwei received his PhD in 2015 from our department, funded by a University of Sheffield Scholarship. His research involves two main areas: highly efficient structural layout/topology optimization methods and novel limit analysis methods using discontinuity layout optimization.
After completing his PhD, Linwei worked as a software developer at LimitState Ltd, where he was offered many opportunities to disseminate his research outcome to practitioners and researchers by developing user-friendly software tools, such as LimitState: SLAB, a fast slab limit analysis tool used by many prominent engineering consultants (e.g. AECOM, Amey and Kier); and LimitState: FORM, an interactive layout/topology optimization tool to design 3D printed light-weight mechanical components for aerospace and automotive applications.
Linwei started his post-doctoral research in our department in 2016, seeking solutions to the climate crisis by developing world-leading structural optimization methods to significantly reduce carbon footprint in multi-storey buildings and long-span canopy roofs. He developed the Peregrine plugin, allowing engineers to use a wide array of powerful structural optimization and rationalization tools to generate material-efficient building designs in their daily commercial design work. His work also led to the development of the www.LayOpt.com webapp, a public educational tool that demonstrates his structural optimization methods to engineers, educators and students.
He is also interested in environmentally friendly building materials such as timber and masonry. He joined a multi-institution project in 2020 to develop efficient limit analysis methods for masonry arch bridges, using the novel discontinuity layout optimization method in conjunction with a homogenization approach.
Years of research experience gave Linwei a wide range of digital skills, e.g., programming, high performance computing, parametric modelling, computer aided design and analysis, etc. In addition to digital work, he also helped make physical models, such as titanium components for aircrafts, timber bridges, and skew masonry bridges, to validate his optimization and analysis methods.
Linwei started his lecturer position in 2022, seeking solutions to the climate crisis by employing optimization methods in structural analysis and design. He is also keen on bringing tangible impact by developing digital tools for engineers and applying them to real-world applications.
- Research interests
-
- Structural layout optimization methods to reduce carbon footprint in multi-storey buildings and long-span canopy roofs with buildability constraints.
- Structural topology optimization for 3D printed metallic components, e.g., connections between building elements and parts for aerospace and automotive applications.
- Multi-material optimization using environmentally friendly building materials such as timber and masonry.
- Novel limit analysis methods to reveal hidden reserves of strength in existing structures, so as to reduce the need to demolish and rebuild.
- Holistic structural optimization and analysis methods to identify structurally efficient reinforcement to maintain the function of existing buildings, and also to design new structures with recycled building materials.
- Publications
-
Journal articles
- Automatic yield-line analysis of out-of-plane loaded masonry cladding panels. Computers & Structures, 305. View this article in WRRO
- Design of optimal truss components for fabrication via multi-axis additive manufacturing. Computer Methods in Applied Mechanics and Engineering, 418, 116464-116464.
- Optimization-driven conceptual design of truss structures in a parametric modelling environment. Structures, 37, 469-482. View this article in WRRO
- LayOpt : an educational web-app for truss layout optimization. Structural and Multidisciplinary Optimization, 64(4), 2805-2823. View this article in WRRO
- Adaptive solution of truss layout optimization problems with global stability constraints. Structural and Multidisciplinary Optimization, 60(5), 2093-2111. View this article in WRRO
- Conceptual design of AM components using layout and geometry optimization. Computers and Mathematics with Applications, 78(7), 2308-2324. View this article in WRRO
- A Python script for adaptive layout optimization of trusses. Structural and Multidisciplinary Optimization, 60(2), 835-847. View this article in WRRO
- Design of optimum grillages using layout optimization. Structural and Multidisciplinary Optimization, 58(3), 851-868. View this article in WRRO
- Automatic Yield-Line Analysis of Practical Slab Configurations via Discontinuity Layout Optimization. Journal of Structural Engineering, 143(7), ---. View this article in WRRO
- Rationalization of trusses generated via layout optimization. Structural and Multidisciplinary Optimization, 52(4), 677-694. View this article in WRRO
- Automatic yield-line analysis of slabs using discontinuity layout optimization. Proceedings of the Royal Society A: Mathematical, Physical and Engineering Sciences, 470(2168), ---. View this article in WRRO
Conference proceedings papers
- Automatic yield-line analysis of out-of-plane loaded masonry cladding panels. Computers & Structures, 305. View this article in WRRO
- Research group
-
Computational Mechanics & Design
Intelligent Infrastructure
- Grants
- PhD opportunities
AI-in-the-loop design optimization of building structures
Building sector accounted for near 40% of energy and process-related CO2 emissions in recent years. To ensure a sustainable built environment, it is vitally important to design buildings that are structurally efficient. Structural layout/topology optimization methods are powerful means of designing highly efficient building structures to tackle the climate crisis. Since the optimization methods are often based on mathematical derivations (e.g., gradient), they require clearly defined design inputs to function correctly. However, real-world scenarios are complicated, so building designs are subject to numerous factors (e.g., aesthetics) that are challenging to incorporate in well-posed mathematical formulations. Moreover, designers may wish to make frequent adjustments in the design loop, since it is not always feasible to foresee all design requirements beforehand. To address this, this project aims to develop a so-called AI-in-the-loop framework, taking advantage of the fast-growing AI technology to aid building optimization. In addition to mathematical optimization algorithms, the framework will integrate an AI-guided intervention step, which adjusts the building designs by, e.g., evolving structural forms and adding/removing design requirements. In this project, the mathematical elements will ensure highly efficient structural designs with significantly reduced CO2 emissions, while the AI elements will help eradicate the practical barriers to stimulate more widespread adoption of innovative buildings in industry. There is an opportunity in this project to develop software tools for industrial users from world-leading UK companies.
Concurrent design optimization of 3D printed truss-like structures and manufacturing configurations
Additive manufacturing (AM, or ā3Dā printing) has developed rapidly in recent years and has the potential to enable fabrication of structurally optimized components that have hitherto been impossible to manufacture. There is a growing interest in 3D printed truss-like structures, not only because they permit light-weight mechanical components for aerospace and automotive applications, but also because they enable innovative building forms in civil and architectural engineering applications. To optimize efficient 3D printed structures, common AM issues (such as the overhang limitations) should be taken into account in the design process. Therefore, a concurrent design optimization approach is proposed, which simultaneously optimizes structural layouts/topologies and manufacturing configurations during the AM process. The aim of this project is to develop concurrent optimization algorithms that can generate (near-)optimum truss-like structures fabricated via modern AM processes, such as the direct energy deposition (DED) and wire arc additive manufacturing (WAAM) approaches. Preliminary research has been conducted and a holistic optimization method was proposed, which, however, focused primarily on 2D problems. This project will therefore extend the methods by optimizing 3D structures, taken from either aerospace/automotive engineering or civil/architectural engineering applications. There is also an opportunity in this project to fabricate physical models and conduct laboratory tests, so as to validate the design methods.
If you're interested in one of these projects, or would like to self-propose a project, please contact Linwei at the above email. Current PhD opportunities in the department can be viewed here.