Multiscale Simulation for Fusion Components
Project period: 2024-2026
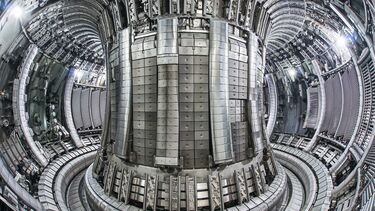
Investigators and researchers
University of Sheffield: Mike McDermott, Shuisheng He
UKAEA: Chris Harrington, Nakul Sashidharan, James Bailey
Background
This project is part of the UKAEA/UoS Partnership Agreement established in 2023. The collaboration in thermal hydraulics is aimed at developing and exploiting a leading set of computational tools and an improved understanding of the physics that will guide the development of fusion components to complement physical experiments possible at the Fusion Technology Facilities. The focus will be on developing multiscale simulation for fusion components through inherent code coupling, supported by high fidelity simulation where possible to assist with verification and validation.
Scope of the project:
Fusion systems have a great level of complexity from the plant-scale to the component scale, all of which must be captured for an accurate representation of the entire system behaviour. Models are required that capture this behaviour without excessive computing and modelling effort and this must feed into digital reactor designs from an early stage in order to influence concept development.
The purpose of this project is to develop a multi-scale modelling framework to enable robust and efficient prediction of the behaviours of the component/system, such as the blankets and divertors within the wider plant. As well as capturing the multi-scale effects, any modelling framework must be capable of appropriately simulating a range of phenomena including the magnetohydrodynamic behaviour of liquid metals within strong magnetic fields.
The new method(s) established will be applied to the analysis and design of fusion plant (e.g., STEP, DEMO) and/or the test facility CHIMERA. Potentially, the new framework will build upon some of the methods employed in the PEGASUS project for digital twinning and may later be integrated with existing full reactor design tools such as BLUEMIRA.
As a supporting workstream, generation of high-fidelity simulation data using methods such as Direct Numerical Simulation (DNS) offers the possibility of “numerical experiments” that complement physical experiments without the operational overhead. This may be particularly valuable for complex flows involving liquid metals and magnetohydrodynamic phenomena. This project will interact with other research initiatives exploring these techniques to support validation of the core simulation predictions and seeking to identify routes to further develop and apply the techniques for fusion.
Research objectives
The overall vision of the UKAEA/UoS collaboration in thermal hydraulics is to develop a multi-scale modelling framework for the simulation of fusion reactor thermal-fluids systems focusing on the blanket and divertor and to advance the understanding and prediction capabilities of the multi-physics encountered in the cooling systems including magnetohydrodynamics (MHD).
The collaboration seeks to pursue research in a number of directions illustrated below. The aim of the current three-year project is to make progresses in several of those workstreams, particularly including topics 1-3 and 6.
- Component modelling using detailed CFD models. Components which are of particular interest include breeding unit, manifolds and the divertor cooling enhancement mechanisms. The purpose of such modelling is to investigate the impact of changes of specific design features/modifications and to collect data from sensitivity studies of variable conditions to support the development of correlations used in system-level simulations.
- Development of a multi-scale system modelling framework for the breeding blanket and associated plant system. This modelling framework is developed using OpenModelica as a platform and is currently modelling the Water-Cooled Liquid-Lead Test Blanket Module (WCLL-TBM) to be implemented in ITER for baseline model development.
- Development of correlations pertinent to fusion applications and 1D/2D models for the predictions of local phenomena. Examples include correlations for friction/heat transfer accounting for MHD, and 2D conduction/natural convection model accounting for magneto-convection in the liquid metal breeding media. Coarse grid CFD, such as Sub-Channel CFD, may also be explored to improve the modelling of a sub-system. Data generated from workstreams 1 or 7 maybe used together with AL/ML tools if relevant.
- Coupling/embedding high-fidelity CFD models with the system modelling package.
- Coupling/integration of the new system package with existing full reactor design tools such as BLUEMIRA.
- Cases studies.
- Study of turbulent flow physics including MHD using direct numerical simulation (DNS), see projects: MHD Fundamental and MHD Application.
Publications
- M. McDermott, S. He, C. Harrington, N. Sashidharan and J. Bailey. Thermal-Hydraulic Assessment of the Water-Cooled Liquid-Lead Test Blanket Module Water Cooling System via OpenModelica, submitted to 21st International Topical Meeting on Nuclear Reactor Thermal Hydraulics (NURETH-21), 31 August – 5 September 2025, Busan, South Korea.