Optimising rail grinding practice for premium rail materials
The University of Sheffield, in partnership with British Steel, is optimising the current rail grinding parameters for balancing productivity and surface integrity for the standard and harder premium rail grades currently used on the track.
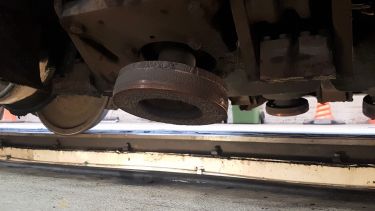
Railway grinding is currently carried out using bespoke trains equipped with a series of vitreous bonded grinding stones that are used to remove material from the railway track. Grinding is carried out in two different modes: preventive grinding - used to take off small amounts of material to return track to its optimum profile ensuring good wheel/rail contact helping to reduce damage and maintain ride comfort; corrective grinding – used to remove damage on rail such as rolling contact fatigue (RCF) cracks.
There is very little science behind the choice of rail grinding parameters which has led to higher forces and speeds being used for the grinding stones than necessary. This can lead to high heat generation and the steel microstructure changing to form brittle martensite, so called “white etching layer” (WEL) on the rail surface. WEL is an initiation point for crack growth and the formation of squat damage which is now bigger problem for European railways than RCF.
The aim of this project, sponsored by British Steel is to commission a new test rig for rail grinding research and establish grinding parameters for standard and harder more durable premium rails, to ensure that material can be removed as required, but with minimal WEL creation.
People involved
Lucas Biazon Cavalcanti