Immobilising Japan’s plutonium
Our researchers have shared the latest strategies for plutonium immobilisation with visitors from the Japanese Citizens' Nuclear Information Center (CNIC).
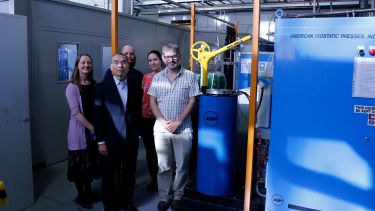
During their visit to Sheffield on 13 September the delegation met with Professor Neil Hyatt and other researchers from the Energy Institute at the University of Sheffield. The Energy Institute has an international reputation in research on plutonium immobilisation for disposal. The visit aimed to investigate effective strategies for plutonium disposal with Sheffield researchers sharing the latest technical perspectives in this area.
The topic of civil plutonium stockpiling in Japan is particularly sensitive due to the proliferation risk of the material. Following the accident at Fukushima, the opportunity for Japan to reuse plutonium has diminished because the full reactor fleet is not expected to restart. This has led to an extensive stockpile of plutonium. The largest portion of Japan's 47 tons of plutonium is held in the UK and the visitors were interested to hear a variety of opinions on what could be done with it.
CNIC's Co-Director, Hideyuki Ban, said "MOX programs around the world are running into trouble, and the situation in Japan has become especially problematic since the Fukushima disaster. Burning 47 tons of plutonium as MOX fuel will take an extremely long time and the government needs to look for more realistic disposal strategies. What we saw here at Sheffield today was a very impressive demonstration of how this can be done. We hope that dialogues between our two countries will progress on different levels, as Japan is also in great need of cost-effective and safe solutions for our plutonium stockpile.”
The UK has the largest stockpile of separated plutonium under civil safeguards, anywhere in the world. The current UK Government is still to make a final decision on whether to reuse this material to fuel a new fleet of nuclear reactors, or whether to immobilise and dispose of it as waste. Indefinite storage of plutonium is not a sustainable option, due to the need to periodically replace degraded packaging. There are several challenges in implementing methods for plutonium reuse so alternative management options are required.
Researchers at the Energy Institute are finding solutions to this challenge by developing the materials and processes required to immobilise and dispose of the plutonium stockpile.
Plutonium-239 will almost fully decay after 240,000 years. This is a long time in human terms but is relatively short period in comparison with geological events. Minerals which survive over geological time frames provide an excellent synthetic material target for plutonium immobilisation. One such material is zirconolite, of which elements have been dated in excess of 500 million years.
Sheffield researchers, supported by the Nuclear Decommissioning Authority and Engineering and Physical Science Research Council, are developing a novel technology to minimise plutonium release from the disposal system. They have developed technologies based on natural zirconolite, in partnership with the National Nuclear Laboratory and Australian Nuclear Science and Technology Organisation.
Researchers are applying high temperatures and pressure to create a reaction to in order to create a material in which plutonium is dispersed. The reaction takes place inside a sealed stainless steel can which acts as the primary container for the waste. By harnessing this technology Sheffield researchers have developed a unique furnace system suitable for processing radiological materials - the first of its kind in the world.
Professor Neil Hyatt, Department of Materials Science and Engineering, said “The work that we are doing to develop a pathway to safely disposing of the UK plutonium stockpile, could equally be applied to material stored for Japan in the UK from reprocessing of its nuclear fuels. We are confident in the fundamental science and engineering principles of the approach and in the long term safety of the ceramic wasteform in geological disposal. The next steps will be to develop a pilot scale demonstration process to prove we can join together all the individual steps of the manufacturing process and the safety case to operate the facility”.