Dry electrode battery printing
A revolutionary fully dry electrode printing process that offers custom shapes with lower capital costs, faster production cycles and significant energy savings.
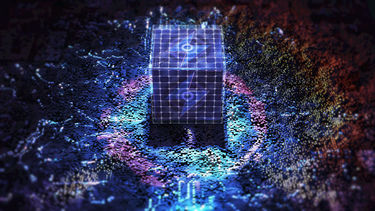
We are looking for anode manufacturers and battery manufacturers interested in exploring how our technology could add value to their products and processes.
Background
Traditional battery electrode manufacturing is energy-intensive, relying heavily on solvent-based processes that not only increase costs but also slow down production. The growing demand for energy-efficient, sustainable, and custom-designed batteries in sectors such as consumer electronics and electric vehicles requires a shift in manufacturing methods.
Solution
At Xerode, we have developed a game-changing solution for battery manufacturing. By eliminating the need for solvents in the electrode printing process, we reduce energy consumption, cut production times, and enable highly customised battery designs for various applications including wearables, consumer electronics and niche electronics. Our name is inspired by xēros (Greek for dry) and electrode = dry electrode, or "Xerode".
Xerode’s innovative dry electrode manufacturing process transforms battery materials into toner-like substances, allowing them to be printed directly onto substrates using electrophotography such as laser printers. This flexible, modular manufacturing approach enables rapid prototyping and custom designs tailored to specific performance requirements, making it a versatile solution for both small-scale and large-scale battery manufacturers.
Benefits
- Energy savings: no drying process is needed, reducing energy consumption and resulting in a smaller hardware footprint.
- Lower capital costs: a modular, scalable system that minimises initial investment.
- Custom design: flexible electrode shapes and performance attributes tailored to a wide range of applications.
- Fast, flexible manufacturing: different geometries can be produced on the same printer.
- Safety: no harmful solvents are involved.
- Time to market: rapid prototyping, enabling faster product to market.
Development status and intellectual property
Xerode has successfully demonstrated the feasibility of the dry printing process for electrode manufacturing, currently at Technology Readiness Level (TRL) 3-4. We anticipate progressing to TRL 5-6 by early 2025. Patents protecting our formulations and manufacturing process are currently being filed.