Dr Shuwen Wen
BSc (Hons), MSc, PhD
Advanced Manufacturing Research Centre
Research Lead
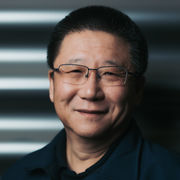
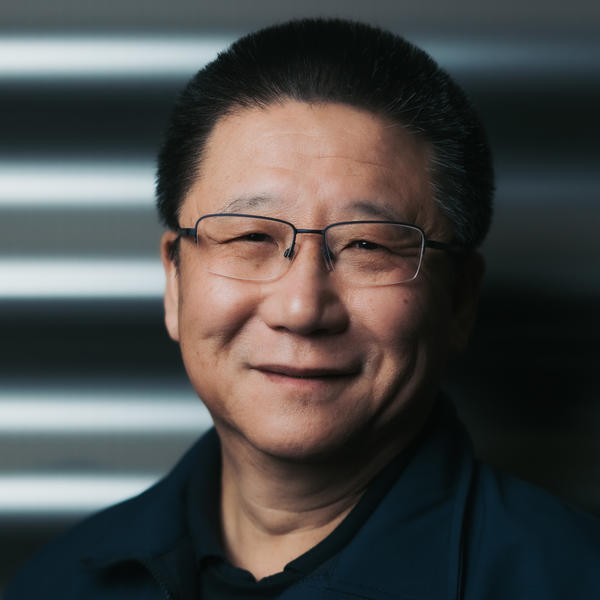
Full contact details
Advanced Manufacturing Research Centre
AMRC Castings
Brunel Way
Rotherham
S60 5TZ
- Profile
-
Shuwen is the Research Lead of the AMRC Castings Group. Joining the AMRC in May 2022, Shuwen brought in a breadth of valuable knowledge and technological expertise from his nearly 30 years of working experience both at academic / research institutions and in industry, including metals solidification processing technologies, casting and metalforming process technologies, process modelling and simulation, manufacturing process induced residual stress prediction, characterization and control. Shuwen’s latest effort is devoted to the development of R&D portfolio for the AMRC Castings Group, primarily focusing on sustainability, digitalisation, and understanding of casting residual stress and its influence on post-cast processing and in-service performance of cast structures.
Currently Shuwen is a Visiting Professor in the Department of Engineering at Leicester University. He is also a member of the editorial board and section editorial board (Computation and Simulation on Metals) for the open access journal Metals, published monthly online by MDPI, and editor of the topic subject on “Numerical Modelling on Metallic Materials” (https://www.mdpi.com/topics/modeling_metallic).
- Research interests
-
Innovative castings and casting process R&D
Digital and sustainable foundry solutions
Improvement of quality, property and integrity of cast structures
Melt cleanliness, castability and recyclability of metals and alloys
Foundry process LCA
Residual stress characterization and control
Numerical modelling and simulation
- Publications
-
Journal articles
- Experimental Characterisation and Numerical Modelling of Residual Stresses in a Nuclear Safe-End Dissimilar Metal Weld Joint. METALS, 11(8).
- Effect of friction stir processing and subsequent annealing on microstructure and mechanical properties of a metastable β-Zr alloy. Materials Science and Engineering: A, 822, 141660-141660.
- Getting the Strain Under Control: Trans-Varestraint Tests for Hot Cracking Susceptibility. Metallurgical and Materials Transactions A, 50(4), 1748-1762.
- A Three-Stage Mechanistic Model for Solidification Cracking During Welding of Steel. Metallurgical and Materials Transactions A, 49(5), 1674-1682.
- Investigation of post-weld rolling methods to reduce residual stress and distortion. Journal of Materials Processing Technology, 247, 243-256.
- The role of Ti carbonitride precipitates on fusion zone strength-toughness in submerged arc welded linepipe joints. Materials Science and Engineering: A, 622, 194-203.
- High pressure rolling of low carbon steel weld seams: Part 2 – Roller geometry and residual stress. Science and Technology of Welding and Joining, 18(1), 84-90.
- High pressure rolling of low carbon steel weld seams: Part 1 – Effects on mechanical properties and microstructure. Science and Technology of Welding and Joining, 18(1), 76-83.
- Multiscale, Multiphysics Numerical Modeling of Fusion Welding with Experimental Characterization and Validation. JOM, 65(1), 99-106.
- Neutron Diffraction Analysis of Complete Residual Stress Tensors in Conventional and Rolled Gas Metal Arc Welds. Experimental Mechanics, 53(2), 195-204.
- Effect of high pressure rolling on weld-induced residual stresses. Science and Technology of Welding and Joining, 17(5), 394-401.
- Residual strain measurement for arc welding and localised high-pressure rolling using resistance strain gauges and neutron diffraction. The Journal of Strain Analysis for Engineering Design, 47(8), 576-586.
- Experimental measurement of biaxial thermal stress fields caused by arc welding. Journal of Materials Processing Technology, 212(4), 962-968.
- Rolling to control residual stress and distortion in friction stir welds. Science and Technology of Welding and Joining, 15(6), 440-447.
- Residual stress engineering in friction stir welds by roller tensioning. Science and Technology of Welding and Joining, 14(2), 185-192.
- Modelling mechanical property recovery of a linepipe steel in annealing process. International Journal of Plasticity, 25(6), 1049-1065.
- Finite element modelling: a solution to seam end cracking?. Science and Technology of Welding and Joining, 11(2), 191-199.
- Finite Element Modelling of Residual Stress in Pipe Welds. Strain, 37(1), 15-18.
- Finite element modelling of a submerged arc welding process. Journal of Materials Processing Technology, 119(1-3), 203-209.
- Roll pass evaluation for three-dimensional section rolling using a simplified finite element method. Proceedings of the Institution of Mechanical Engineers, Part B: Journal of Engineering Manufacture, 211(2), 143-158.
- Finite Element Analysis of Four-Roll Pass Cold Rolling. Proceedings of the Institution of Mechanical Engineers, Part B: Journal of Engineering Manufacture, 206(2), 133-141.
- Numerical Modelling on Metallic Materials. Metals, 15(4), 423-423.
- Revealing internal flow behaviour in arc welding and additive manufacturing of metals. Nature Communications, 9(1).
- Initiation and growth kinetics of solidification cracking during welding of steel. Scientific Reports, 7(1).
Conference proceedings papers
- Manufacture and Qualification of Small Diameter / Thickwall Reelable DSAWL Linepipe. Volume 3: Operations, Monitoring and Maintenance; Materials and Joining, 26 September 2016 - 30 September 2016.
- Manufacture and qualification of small diameter / thickwall reelable DSAWL linepipe. Proceedings of the Biennial International Pipeline Conference, IPC, Vol. 3
- On the Relationship of Microstructure, Toughness, and Hardness Properties in a Submerged Arc Welded API-5L Grade X65 Pipeline Steel Section. Volume 5: Materials Technology; Petroleum Technology, 8 June 2014 - 13 June 2014.
- Neutron Diffraction Measurement of Weld Residual Stresses in an UOE Linepipe Subjected to Mechanical Expansion. Volume 3: Materials Technology; Ocean Space Utilization, 9 June 2013 - 14 June 2013.
- An integrated framework for multi-scale multi-physics numerical modelling of interface evolution in welding. IOP Conference Series: Materials Science and Engineering, Vol. 33 (pp 012029-012029)
- Finite Element Modelling of Deepwater UOE Linepipe Manufacturing. Volume 3: Materials Technology; Jan Vugts Symposium on Design Methodology of Offshore Structures; Jo Pinkster Symposium on Second Order Wave Drift Forces on Floating Structures; Johan Wichers Symposium on Mooring of Floating Structures in Waves, 19 June 2011 - 24 June 2011.
- The effect of pre-weld rolling on distortion and residual stress in fusion welded steel plate. Materials Science Forum, Vol. 681 (pp 486-491)
- Modelling of Damage Reduction and Microstructure Evolution by Annealing. AIP Conference Proceedings
Other
- Experimental Characterisation and Numerical Modelling of Residual Stresses in a Nuclear Safe-End Dissimilar Metal Weld Joint. METALS, 11(8).
- Grants
-
EU CAJU, HEAVEN – Hydrogen Engine Architecture Virtually Engineered Novelly, (Co-I), 2023 – 2026, £480,062, (ITP Aero UK).
ATI, Ultra Clean Cast DLMM, (Co-I), 2023 – 2026, £287,679, (Sylatech, Alloyed & Cranfield University).
HVMC, High Value Recycling Guide, (Co-I), 2023 – 2024, £125,000.
HVMC, Manufacturing Process Energy Reduction Guide, (Co-I), 2023 – 2024, £100,000.
HVMC, Assessing the Value of Data for Sustainability Decision Making and Process Sustainability database, (Co-I), 2023 – 2024, £48,000.
- Teaching activities
-
PhD supervision (completed):
- Huan Li, 2009, Birmingham University. Industrial supervisor.
- Harry Coules, 2012, Cranfield University. Industrial supervisor.
- Luis Daniel Cozzolino, 2013, Cranfield University. Industrial supervisor.
- Lee Aucott, 2015, Leicester University, Industrial supervisor.
- Dimitrios Statharas, 2019, Leicester University, Industrial supervisor.