Dr Pete Crawforth
MEng, PhD
Advanced Manufacturing Research Centre
Technical Fellow
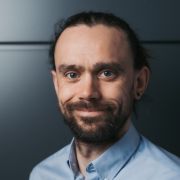
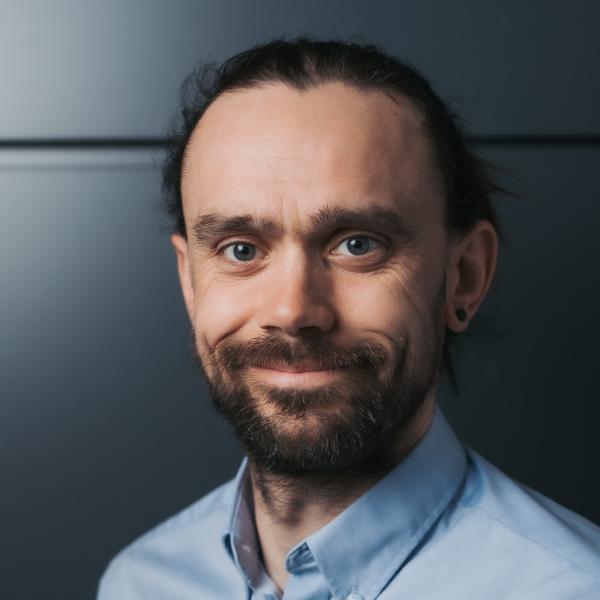
Full contact details
Advanced Manufacturing Research Centre
Factory of the Future, Advanced Manufacturing Park
Wallis Way, Catcliffe
Rotherham
S60 5TZ
- Profile
-
Professor Pete Crawforth leads the subtractive technology group which principally focuses on cross cutting low TRL (1-4) themes that bridge the gap between state-of-the-art subtractive processes and industry ready implementation strategies. The team currently includes specialists in materials characterisation, sustainability, digital, zero defect and agile machining.
Pete holds an undergraduate degree in Mechanical Engineering from the University of Sheffield. In 2014, he completed a PhD in Materials Science and Engineering at the same institution. His project studied the emerging subject of metallurgical analysis of machined titanium. More specifically, the mechanisms of microstructural damage were investigated in order to rationalise the formation of damaged structures.
- Qualifications
-
MEng, PhD
- Research interests
-
Pete’s research interests include: Developing Novel Hole Generation Strategies for Aircraft Assemblies.
- Publications
-
Journal articles
- A model for chatter stability enhancement through lattice support structures. Procedia CIRP, 133, 525-530. View this article in WRRO
- Non-destructive on-machine inspection of machining-induced deformed layers. CIRP Journal of Manufacturing Science and Technology, 52, 296-306.
- Non-destructive X-ray diffraction surface integrity inspection of an aeroengine component. Procedia CIRP, 123, 357-362.
- On the surface integrity of machined aero-engine grade Ni-based superalloy billets produced by the field-assisted sintering technology (FAST) route. Procedia CIRP, 123, 310-315.
- Rapid acquisition of digital fingerprints of Ti-6Al-4V macrotexture from machining force measurement data. Materials Characterization, 207, 113550-113550.
- Insights in α-Al2O3 degradation in multilayer CVD coated carbide tools when turning IN718. Wear, 204786-204786.
- Machining performance and wear behaviour of polycrystalline diamond and coated carbide tools during milling of titanium alloy Ti-54M. Wear, 204791-204791.
- The influence of machining induced surface integrity and residual stress on the fatigue performance of Ti-6Al-4V following polycrystalline diamond and coated cemented carbide milling. International Journal of Fatigue, 163, 107054-107054.
- Rapid non-destructive sizing of microstructural surface integrity features using x-ray diffraction. NDT & E International, 102682-102682.
- An evaluation of non-destructive methods for detection of thermally-induced metallurgical machining defects. Procedia CIRP, 108, 7-12.
- On the mechanism of crater wear in a high strength metastable β titanium alloy. Wear, 484-485, 203998-203998.
- A novel method for investigating drilling machinability of titanium alloys using velocity force maps. Advances in Industrial and Manufacturing Engineering, 100043.
- The effect of forging texture and machining parameters on the fatigue performance of titanium alloy disc components. International Journal of Fatigue, 142. View this article in WRRO
- On deformation characterisation of machined surfaces and machining-induced white layers in a milled titanium alloy. Journal of Materials Processing Technology, 117378-117378.
- Using Machining Force Feedback to Quantify Grain Size in Beta Titanium. Materialia, 100856-100856.
- Machining of directed energy deposited Ti6Al4V using adaptive control. Journal of Manufacturing Processes, 54, 240-250.
- Resource consumption and process performance in minimum quantity lubricated milling of tool steel. Procedia Manufacturing, 43, 463-470.
- The effect of Titanium Alloy Composition and Tool Coating on Drilling Machinability. MATEC Web of Conferences, 321, 13002-13002.
- A Novel Technique to Assess the Effect of Machining and Subsurface Microstructure on the Fatigue Performance of Ti-6Al-2Sn-4Zr-6Mo. MATEC Web of Conferences, 321, 04012-04012.
- Quantitative characterization of machining-induced white layers in Ti–6Al–4V. Materials Science and Engineering: A, 764. View this article in WRRO
- Machining of functionally graded Ti6Al4V/ WC produced by directed energy deposition. Additive Manufacturing, 24, 20-29.
- Destructive and non-destructive testing methods for characterization and detection of machining-induced white layer: A review paper. CIRP Journal of Manufacturing Science and Technology. View this article in WRRO
- On the machinability of directed energy deposited Ti6Al4V. Additive Manufacturing, 19, 39-50.
- On the mechanism of tool crater wear during titanium alloy machining. Wear, 374-375, 15-20.
- Titanium alloy microstructure fingerprint plots from in-process machining. Materials Science and Engineering: A.
Chapters
- Linking Machining Response of Titanium Billet to Upstream Thermomechanical Processing, Proceedings of the 13th World Conference on Titanium (pp. 1649-1654). John Wiley & Sons, Inc.
Conference proceedings papers
- A Novel Spindle Speed and Angle Estimation Strategy in Multi-material Robotic Drilling. 2024 IEEE 20th International Conference on Automation Science and Engineering (CASE) (pp 1222-1227), 28 August 2024 - 1 September 2024.
- Pixel-based Hole Quality Evaluation in Robot Drilling Manufacturing Process. 2024 IEEE 22nd International Conference on Industrial Informatics (INDIN) (pp 1-6), 18 August 2024 - 20 August 2024.
- Surface roughness response to drilling of Ti-5Al-5Mo-5V-3Cr using Ti-Al-N PVD coated and uncoated WC/Co tools. Procedia CIRP, Vol. 87 (pp 170-175). Mondragón, Spain, 1 June 2020 - 5 June 2020. View this article in WRRO
- Non-destructive detection of machining-induced white layers in ferromagnetic alloys. Procedia CIRP, Vol. 87 (pp 420-425). Mondragon, Spain, 1 June 2020 - 5 June 2020. View this article in WRRO
- The Influence of Alloy Chemistry on the Cutting Performance and Deformation Kinetics of Titanium Alloys During Turning. Procedia CIRP, Vol. 45 (pp 151-154) View this article in WRRO
- Machining of Additively Manufactured Parts: Implications for Surface Integrity. Procedia CIRP, Vol. 45 (pp 119-122) View this article in WRRO
- Predicting Chemical Wear in Machining Titanium Alloys Via a Novel Low Cost Diffusion Couple Method. Procedia CIRP, Vol. 45 (pp 219-222)
- A model for chatter stability enhancement through lattice support structures. Procedia CIRP, 133, 525-530. View this article in WRRO
- Research group
-
Machining